Understanding Die Casting Products: Revolutionizing Metal Fabrication
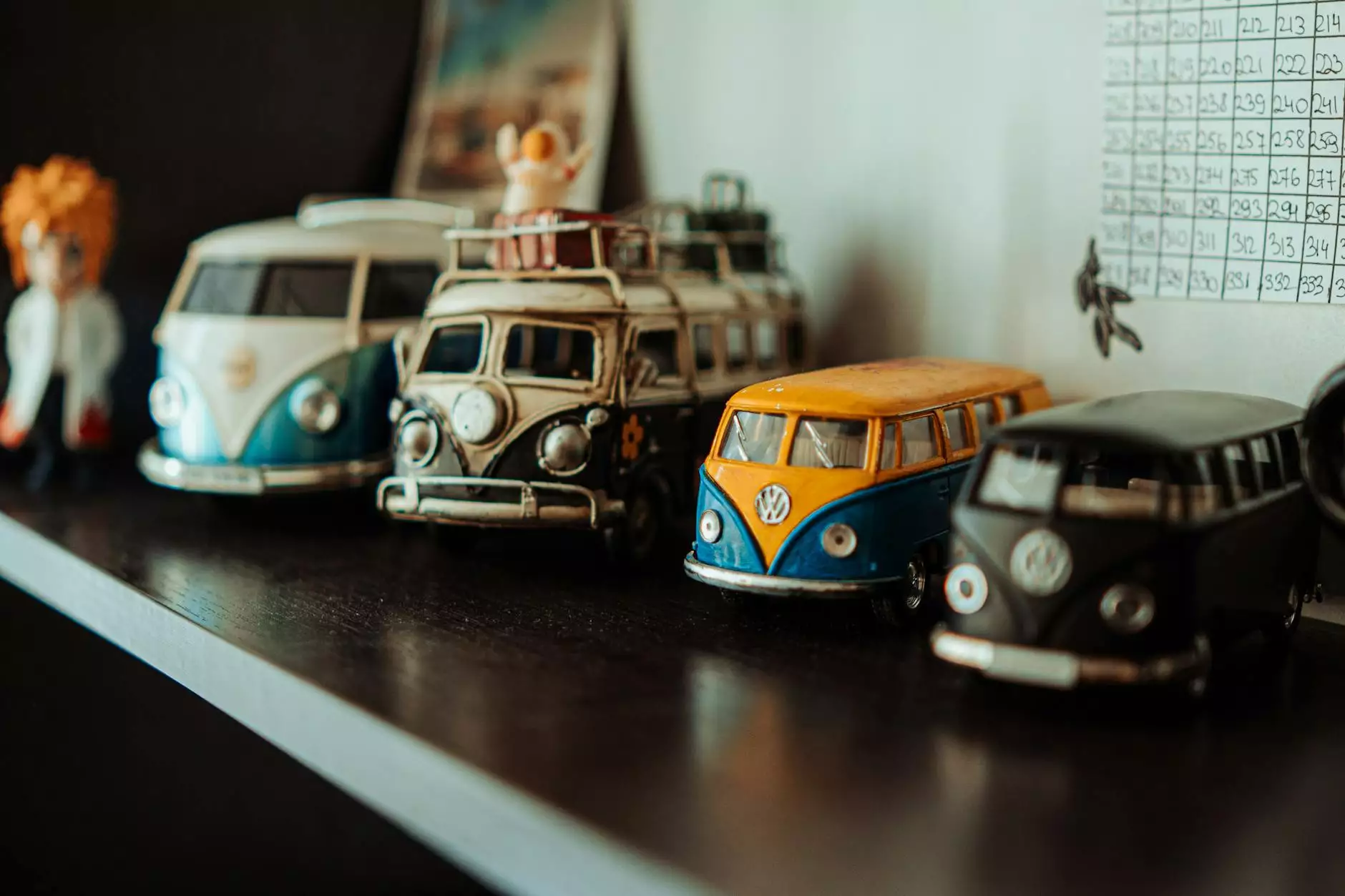
In the ever-evolving landscape of manufacturing, die casting products have emerged as a key player in precision metal fabrication. These innovative products not only enhance production efficiency but also improve the overall quality of manufactured goods. In this article, we delve into the fundamentals of die casting, its advantages, specific applications, and why it has become a cornerstone in the industry.
What is Die Casting?
Die casting is a manufacturing process that involves forcing molten metal under high pressure into a mold cavity. This method allows for the creation of complex shapes and designs that are often found in numerous applications, from automotive components to intricate electronic casings. The molds used in die casting are made from hard materials, typically steel or iron, which enables them to withstand the intense pressure and temperature involved in the process.
The Die Casting Process
The die casting process consists of several key stages:
- Preparation of the die: The first step involves preparing the mold, which is meticulously designed to achieve the desired shape of the product.
- Melting the metal: Metals, such as aluminum, magnesium, or zinc, are heated until they reach a molten state.
- Injection: The molten metal is injected into the die under high pressure. This step is crucial as it ensures that the mold is filled completely, preventing any voids or air pockets.
- Cooling: After the metal has filled the die, it is allowed to cool for a short period, during which it solidifies into the desired shape.
- Ejection: Once cooled, the newly formed product is ejected from the die, and the process can be repeated quickly for mass production.
Advantages of Die Casting Products
Die casting offers a plethora of advantages that make it a popular choice for manufacturers in various industries. Here are some of the key benefits:
- High precision and detail: Die casting products achieve a high level of dimensional accuracy, making them suitable for intricate designs.
- Efficient mass production: Once the molds are created, the die casting process allows for rapid production, reducing time and labor costs.
- Enhanced strength and durability: The high pressure used in die casting results in products that have superior mechanical properties compared to those produced by other methods.
- Materials versatility: Die casting can be performed with a wide range of metals, making it adaptable to various applications.
- Reduced waste: The process is highly efficient, with minimal wasted materials, resulting in a more eco-friendly manufacturing approach.
Applications of Die Casting Products
The versatility of die casting products allows them to be utilized in a multitude of industries, including:
1. Automotive Industry
The automotive sector is one of the largest consumers of die casting products. Components such as gearbox housings, engine blocks, and decorative parts benefit significantly from the precision and weight reduction offered by die casting.
2. Electronics
In the electronics industry, die casting is used to produce enclosures and housings for devices. The excellent thermal conductivity of metals like aluminum makes them ideal for heat dissipation in electronic gadgets.
3. Aerospace
The aerospace industry demands high-strength components that also weigh less. Die casting provides the necessary attributes for parts used in aircraft, enhancing fuel efficiency and safety.
4. Consumer Products
From kitchen appliances to furniture fittings, die-cast products are prevalent in consumer goods, offering durability and aesthetic appeal.
Choosing the Right Die Casting Manufacturer
When selecting a die casting manufacturer, it is essential to consider several factors to ensure you receive high-quality products:
- Experience and expertise: A manufacturer with a solid track record in the industry will likely deliver superior results.
- Quality assurance measures: Look for companies that implement strict quality control processes to maintain high standards.
- Technological capabilities: Modern die casting techniques, such as vacuum die casting and hot chamber die casting, can enhance product quality.
- Customer service: Good communication and support are crucial for a successful partnership.
Environmental Considerations in Die Casting
As industries become more environmentally conscious, die casting also adapts. The process can be made more sustainable by:
- Using recycled materials: Many die casting manufacturers now incorporate recycled metals, reducing the demand for raw materials.
- Energy efficiency: Investing in energy-efficient machinery can significantly lower the carbon footprint of die casting operations.
- Waste reduction tactics: Implementing measures to minimize scrap and cycle times contributes to a greener manufacturing process.
Future Trends in Die Casting
The future of die casting is promising, with several trends reshaping the industry:
- Automation: Increasing adoption of robotic technology in the die casting process is enhancing efficiency and reducing production time.
- 3D printing for mold making: 3D printing technology is revolutionizing mold production, allowing for faster design iterations and reduced costs.
- Smart manufacturing: The integration of IoT and data analytics is providing manufacturers with valuable insights to optimize die casting operations.
Conclusion
In conclusion, die casting products play a pivotal role in the metal fabrication industry, providing numerous advantages such as precision, efficiency, and versatility. As businesses like Deep Mould continue to innovate within this field, we can expect even greater advancements that will influence various sectors. From automotive to aerospace, the future of die casting is not just about the products but also about creating more sustainable manufacturing practices that will benefit the environment and the economy alike.
Discover Die Casting Products Today!
If you're looking for high-quality die casting products or need more information on how they can benefit your business, connect with the experts at Deep Mould. Our commitment to quality and innovation ensures that you receive the best solutions tailored to your specific needs.