Exploring the World of Metal Turning Lathe Parts
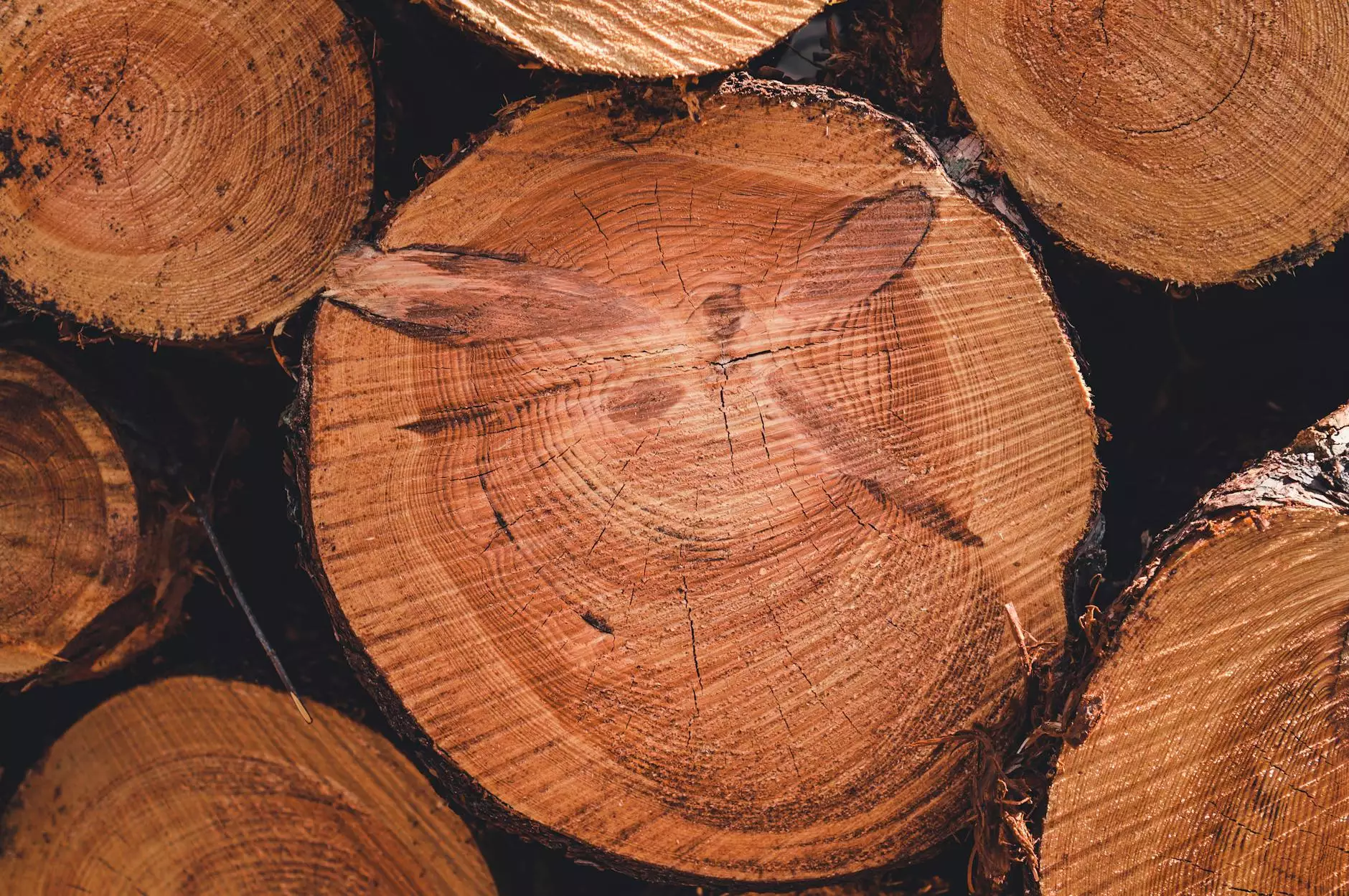
When it comes to precision engineering, metal turning lathe parts play a pivotal role in the manufacturing process. These components are essential for the creation of a wide range of products, from intricate machine parts to robust industrial components. This article delves deep into the various aspects of metal turning lathe parts, highlighting their importance, types, applications, and best practices involved in their use and manufacturing.
What are Metal Turning Lathes?
A lathe is a machine tool that rotates a workpiece on its axis to facilitate the shaping of the material. Metal turning lathes are specifically designed to work with metal as the primary material. They can perform a variety of operations, including turning, facing, drilling, and threading. By using cutting tools, the lathe removes material to achieve a desired shape and finish.
The Mechanism of a Metal Turning Lathe
The basic components of a lathe include:
- Headstock: The headstock houses the spindle which holds the workpiece and drives its rotation.
- Tailstock: Stabilizes the other end of the workpiece and can house tools for drilling.
- Bed: The bed is the base of the lathe, providing support for the headstock, tailstock, and carriage.
- Carriage: The carriage holds the cutting tool and moves it along the workpiece as it rotates, affecting how much material is cut away.
- Apron: Attached to the carriage, it houses the controls for lateral movement of the cutting tool.
Types of Metal Turning Lathe Parts
The effectiveness of a lathe largely depends on its metal turning lathe parts. Here are some of the key components that exhibit considerable significance:
1. Chuck
The chuck is a clamping device that holds the workpiece securely in place. There are various types of chucks:
- Three-Jaw Chuck: Ideal for round objects, it provides uniform clamping pressure.
- Four-Jaw Chuck: Best for irregularly shaped pieces, allowing independent adjustments for each jaw.
- Collet Chuck: Offers precise gripping of smaller workpieces.
2. Tool Post
The tool post secures cutting tools in place and allows adjustments to their position. Quick-change tool posts enhance efficiency by permitting fast tool swapping during operations.
3. Cutting Tools
Cutting tools come in various shapes and materials, each designed for specific tasks. Common types include:
- High-Speed Steel (HSS): Versatile and cost-efficient for general use.
- Carbide Tipped: Enhances durability and effectiveness for harder materials.
- Ceramic and CBN Tools: Suitable for high-speed machining applications.
4. Tailstock Spindle
The tailstock spindle allows for the use of drilling and tapping tools, providing additional functionality to the lathe. It can be adjusted to accommodate various workpiece lengths.
Applications of Metal Turning Lathe Parts
Understanding the applications of metal turning lathe parts is crucial for optimizing their use in production processes. They are widely employed across various industries:
1. Aerospace Manufacturing
In the aerospace sector, precision is paramount. Metal turning lathe parts are used to create components like turbine blades, shafts, and gears, ensuring they meet stringent safety and performance standards.
2. Automotive Industry
Automotive manufacturers utilize turning lathes to produce critical engine parts, transmission components, and custom fittings that require precise tolerances.
3. Medical Devices
Medical technology demands high precision for components that fit in instrumentation, implants, and surgical tools. Metal turning lathes are key to producing these devices safely and effectively.
4. Robotics and Automation
Robotics rely on durable and precise components for functionality. Metal turning lathes are integral in manufacturing parts like actuators, gears, and chassis for robotic systems.
Best Practices for Using Metal Turning Lathe Parts
To ensure the longevity and functionality of metal turning lathe parts, it is essential to follow best practices:
1. Regular Maintenance
Scheduled maintenance keeps the lathe and its parts in optimal working condition. This includes:
- Cleaning: Remove chips and debris after each use to prevent wear.
- Lubrication: Regularly oil moving parts to reduce friction and wear.
- Inspection: Check parts for any signs of damage or excessive wear.
2. Choosing the Right Materials
Selecting the appropriate materials for cutting tools and workpieces enhances performance and lifespan. Considerations should include:
- Material Hardness: Ensure tool materials are suitable for the hardness of the workpiece.
- Compatibility: Match tool coatings and materials to the specific application.
3. Training and Skill Development
Operators should receive comprehensive training on using metal turning lathe parts effectively. Familiarity with machining practices, safety protocols, and the specifications of each component leads to improved outcomes.
Future Trends in Metal Turning and Machining
The landscape of metal turning and machining is constantly evolving. Technological advancements and innovations are shaping the future of metal turning lathe parts:
1. Automation and CNC Technology
Computer Numerical Control (CNC) lathes are becoming standard, enhancing precision and reducing human error. These lathes can operate autonomously, allowing for increased production speeds and efficiency.
2. Additive Manufacturing Integration
Integrating additive manufacturing techniques with traditional metal turning allows for more complex geometries that were previously difficult or impossible to produce. This hybrid approach is revolutionizing the way parts are manufactured.
3. Sustainable Practices
As industries push towards sustainability, manufacturers are implementing greener practices, such as using eco-friendly lubricants and recycling metal shavings. These initiatives are essential for reducing the environmental impact of metal machining.
Conclusion
In conclusion, metal turning lathe parts are crucial components in the manufacturing industry, facilitating the creation of precision parts across various sectors. By understanding their functions, applications, and best practices, manufacturers can optimize their processes and improve product quality. As technology continues to advance, staying informed about trends and developments will ensure businesses remain competitive. At deepmould.net, we are committed to providing high-quality metal fabrication services tailored to meet your specific needs in this evolving landscape.